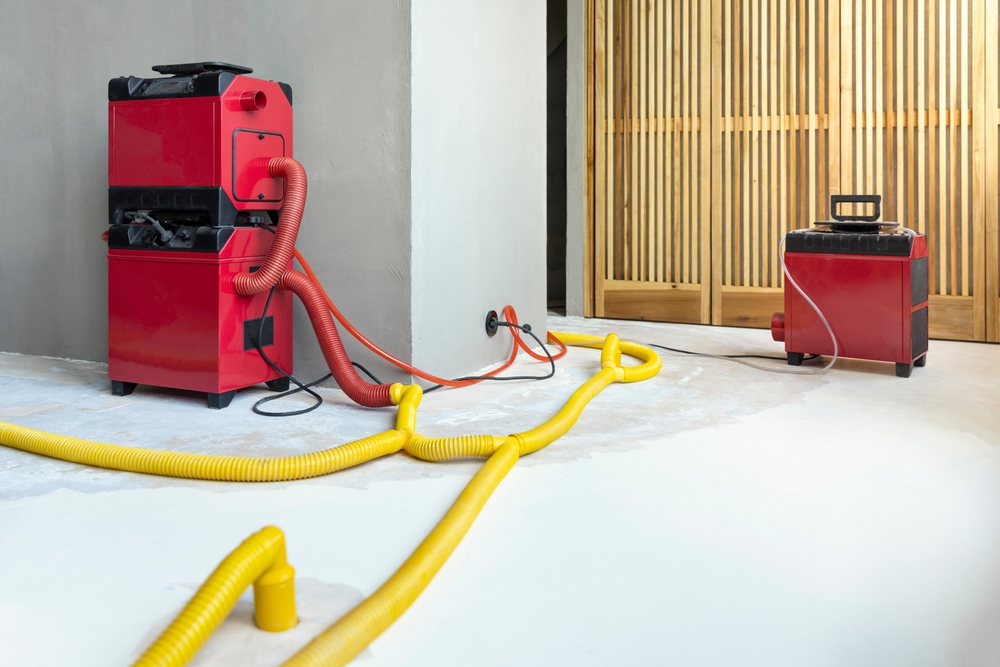
What is Condenser Drying?
Industrial refrigeration systems are complex setups designed to provide efficient cooling for various industrial processes. They consist of several key components, each playing a vital role in the refrigeration cycle. The primary components include compressors, condensers, evaporators, expansion valves, and refrigerants. Compressors are responsible for compressing refrigerant gases, raising their pressure and temperature. Condensers then cool and liquefy the refrigerant, releasing heat to the surroundings. Evaporators absorb heat from the target environment, causing the refrigerant to evaporate and thus cooling the area. Expansion valves regulate the flow of refrigerant into the evaporator, controlling the cooling process. Refrigerants are the medium that cycles through these components, undergoing phase changes to facilitate heat transfer. Each component must work in harmony for the system to function efficiently, ensuring optimal cooling performance in industrial settings.
Industrial refrigeration systems play a crucial role in various sectors, including food processing, pharmaceuticals, cold storage, and HVAC. These systems are essential for preserving perishable goods, maintaining controlled environments for manufacturing processes, and supporting research and development activities. The efficiency and reliability of industrial refrigeration systems depend heavily on the quality and compatibility of their components. Therefore, selecting the right components and ensuring proper installation and maintenance are vital for maximizing system performance and longevity. Additionally, advancements in technology have led to the development of more energy-efficient and environmentally friendly refrigeration solutions, driving the evolution of industrial refrigeration systems to meet modern demands for sustainability and efficiency.
Industrial refrigeration systems differ from commercial ones primarily in terms of scale, capacity, and application. Industrial systems are typically larger and more powerful, designed to handle the cooling needs of large-scale industrial processes, such as food processing plants, cold storage facilities, and chemical manufacturing plants. They often operate continuously and are capable of providing precise temperature control over large areas or volumes.
In contrast, commercial refrigeration systems are typically smaller and less powerful, intended for use in retail stores, restaurants, supermarkets, and other commercial establishments. While they still provide cooling for perishable goods and products, they are generally designed for smaller-scale applications and may not require the same level of precision or capacity as industrial systems. Additionally, commercial systems may have different features and components tailored to the specific needs of the retail or foodservice industry, such as display cases, walk-in coolers, or ice machines.
Many industries rely on industrial refrigeration systems to maintain the quality of products and optimise production processes. The food industry requires refrigeration systems when processing a wide range of products, from agricultural produce to meat, dairy and seafood. Cold chain management keeps products fresh, reducing spoilage and waste, while providing long-term storage and transport for frozen food products. The chemical industry also relies on industrial refrigeration systems, which control temperature during storage, processing and transport of chemicals. Other industries such as power generation, pharmaceuticals, automotive, plastics and metalworking also rely on industrial refrigeration systems to maintain the quality of products, improve the performance of equipment and ensure a reliable production process.
The demand for industrial cooling systems is increasing at a time when businesses continue to improve technology and efficiency to increase productivity and gain a competitive advantage. Therefore, industrial refrigeration systems have become a critical component in many different industries. These systems are vital for industrial applications such as food, chemical, pharmaceutical, automotive, energy and many more. The reliability, durability and energy efficiency of refrigeration systems have become a key performance element for businesses in these industries.
The different types of chillers used in industrial cooling systems are usually selected based on factors such as thermal performance, environmental effects and safety. Here are a few main types commonly used in these systems:
Freons (Hydrofluorocarbons - HFCs): Freons are a type of refrigerant that has long been widely used in industrial refrigeration applications. However, due to their damaging effects on the ozone layer, their use is gradually decreasing due to environmental concerns.
Ammonia (NH3): Ammonia is one of the most widely used refrigerants in industrial refrigeration systems. It is preferred due to its high thermal conductivity and effective cooling capacity. However, it requires careful handling due to the risk of being toxic and explosive.
CO2 (Carbon Dioxide): CO2 has been gaining popularity in industrial cooling systems in recent years. An environmentally friendly option, CO2 has low global warming potential and is seen as a low-cost alternative. It is especially common in supermarkets and food processing plants.
Hydrocarbons (Propane, Isobutane): Hydrocarbons are naturally occurring and environmentally friendly refrigerants. In recent years, they are more preferred in industrial refrigeration systems because they attract attention with their low environmental impact and effective cooling performance.
Industrial refrigeration systems play a critical role in the food industry to ensure safety and quality. These systems ensure that food is stored and transported at the appropriate temperature, reducing the risk of spoilage. However, they not only ensure low temperatures, but also pay attention to factors such as humidity and ventilation. For example, when storing fruit and vegetables, appropriate humidity levels are important to maintain the freshness of the products. Furthermore, ventilation systems help to remove unwanted gases and odours from storage areas so that the flavour and quality of the products are maintained. All these measures show that industrial refrigeration systems are a critical component to ensure food safety and quality.
Industrial refrigeration systems are vital to ensure food safety and quality. These systems provide the necessary environment for the storage and transport of food products at the appropriate temperature. In particular, low temperatures inhibit the growth of bacteria and microorganisms, thus preventing food spoilage. Furthermore, additional factors such as humidity and ventilation control are also important to maintain the freshness and quality of food. For example, when storing sensitive foods such as meat and seafood, low temperatures as well as appropriate humidity levels must be maintained. Therefore, industrial refrigeration systems play a critical role in ensuring reliable and quality products in the food industry.
Maintenance of industrial refrigeration systems is vital to ensure the efficiency and reliability of the systems. These systems need to be cleaned and checked regularly. For example, evaporation coils and fans should be cleaned and checked at regular intervals. Refrigerant levels and pressures should also be monitored regularly and adjusted if necessary. Electrical connections and components should also be checked periodically and serviced as necessary. All these maintenance practices ensure the smooth operation of industrial refrigeration systems and help prevent failures.
Regular maintenance of industrial cooling systems is important to improve the performance and durability of the systems. These maintenance practices include changing filters, checking the oil levels of compressors and cleaning them if necessary. In addition, the tightness of the connections in the system should also be checked regularly. In addition, it is also important to check the thermal insulation and renew it when necessary, as good thermal insulation improves energy efficiency and makes systems run more efficiently. All these maintenance practices ensure the long life and stable operation of industrial refrigeration systems.
Fill out the form to discover the most suitable high-end products for your projects. Contact Us Now.