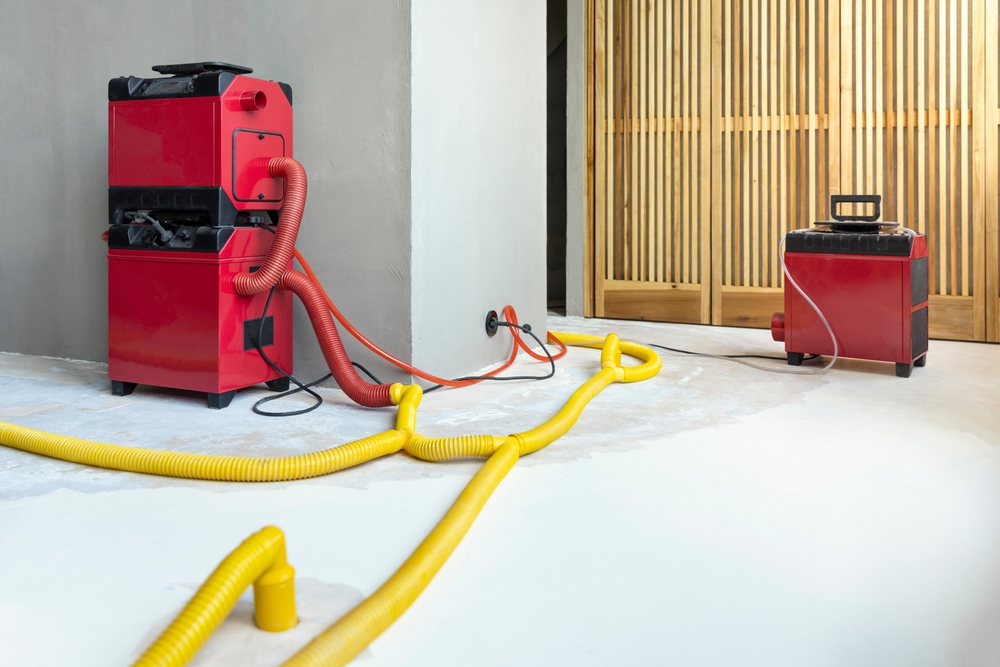
What is Condenser Drying?
A resistor is a component that converts electrical energy into heat and is widely used in various industrial, commercial and domestic applications. Essentially, it is an element that heats up by providing resistance when an electric current passes. This heat enables electrical energy to be converted directly into thermal energy. Resistors are usually manufactured from materials such as metal wire, ceramic or carbon, and their electrical resistance is designed to operate within a certain temperature range.
It is found in homes, especially in hot water producing devices, ovens and heating systems. In industry, it is used in heating processes, drying machines and various production equipment. Correct selection and maintenance are important for the efficient operation of the resistors. Choosing the appropriate type of resistor, especially for different applications, can be critical in terms of energy efficiency and performance. Therefore, choosing a resistor suitable for your usage area will both save energy and extend the life of your devices.
A resistor is a resistance element through which electric current passes, and its basic function is to convert electrical energy into heat energy. The working principle is based on Ohm's Law; that is, when current passes through a resistor, electrical energy is released as heat across the resistor. The internal structure of the resistor usually contains high resistance metal wire or ceramic material. These materials produce high temperatures when they pass electric current. This heat provides the temperature needed by the user by heating the environment around the resistance.
For example, in an electric stove or hot water kettle, the resistance converts the electric current into heat, and this heat causes water to boil or food to cook. In order for the resistor to work efficiently, it must operate at the correct voltage and current values. In addition, proper cooling and maintenance procedures extend the life of the resistor and increase its performance. Therefore, it is of great importance to correctly select and use the resistor according to the requirements of the device in which it is installed.
The basic function of resistors is to convert electrical energy into heat energy. Passing an electric current through a material with high resistance causes this material to heat up and the surrounding environment to warm up. This process is based on Ohm's Law; Electric current passing through the resistor turns into heat depending on the resistor value. For example, resistors in electric stoves, water heaters and various heating devices convert this electrical energy into heat, ensuring the device operates effectively.
Resistors are also used to provide temperature control. Heating elements often work in conjunction with thermostatic controls to help maintain a certain temperature level. This both increases energy efficiency and ensures the safety of the device. They perform essential functions in applications such as cooking food on electric stoves, boiling water in kettles, and providing heat in various industrial processes. Correct selection and maintenance of resistors are important factors affecting the performance of the devices and ensure long-lasting use.
Resistors play a critical role in various industries and offer a wide range of applications. Electric heating devices are one of these sectors. In the home appliance industry, resistors are widely used in products such as electric stoves, water heaters, ovens and heating blankets. These devices make the daily life of users easier while performing indoor heating and cooking processes effectively.
In the industrial field, resistors are used especially in production processes and applications that require temperature control. In sectors such as plastic processing, metal melting and food processing, resistors are used to bring and process materials to certain temperatures. Additionally, in the automotive and aviation industries, resistors are used to warm up the engine and other components and reduce the risk of freezing. Applications in this sector emphasize the ability of resistors to provide reliable and effective thermal management.
The fact that resistors have such a wide range of applications allows them to be designed and optimized in accordance with sectoral needs. This both increases energy efficiency and maximizes the performance of devices and systems.
Resistors come in various types and features used in heating applications. The most common among these types are metal, ceramic and closed resistors. Metal resistors are preferred because they are particularly resistant to high temperatures and long-lasting. They are generally produced from alloys such as iron, nickel or chromium and are used in applications such as electric stoves and water heaters. These types of resistors offer reliable performance thanks to their high thermal conductivity and durability.
Ceramic resistors are preferred in various industrial applications because they distribute heat more evenly and can operate at lower temperatures. Ceramic material is very effective at absorbing and radiating heat and is often used in electric heating devices, dryers and industrial ovens. Closed resistors are used especially in applications requiring high security. These resistances are usually created with heating elements contained in a metal tube and are thus protected from environmental effects. They are commonly found in electric stoves, ovens and laboratory equipment.
Each type of resistor is designed according to specific application needs, and when choosing based on its features, factors such as heating capacity, durability and safety should be taken into account. This diversity enables the resistors to offer a wide range of uses and offers suitable solutions for every sector.
Various types of resistances that you can use at home are designed to meet different needs in daily life. The most common types of household resistors include metal, ceramic and carbon resistors. Metal resistors are known for their durability and rapid heating capacity. It is often used in electric stoves, water heaters and ovens. These resistors can withstand high temperatures and provide reliable performance over long periods of use.
Ceramic resistors are another type that is frequently preferred in home heating applications. These types of resistors are often used in electric heaters, dryers and some kitchen appliances because they distribute heat more evenly and can be effective at lower temperatures. Ceramic material is very effective in absorbing and dissipating heat, which increases energy efficiency and provides more comfortable heating.
Carbon resistors are suitable for those looking for a more innovative solution at home. Carbon-based resistors offer particularly energy-saving heating solutions and are often used in modern electric heaters and radiators. These types of resistors attract attention with their high energy efficiency and low energy consumption.
Each type of resistor is optimized for specific home needs, and when choosing, it is important to determine the most suitable type based on your intended use and energy efficiency.
Industrial type resistors are specially designed for applications requiring high temperatures and durability in industrial processes. These types of resistors have a wide range of uses in heavy industry applications such as metal production, plastic processing, glass and ceramic production. Since they are often used in environments requiring high performance, they are known for their durability and long life. Metal and ceramic based ones are preferred in industrial furnaces and heating systems thanks to their capacity to withstand high temperatures.
The advantages of industrial type resistors include high energy efficiency and excellent temperature control. These resistors help control processes with precision, providing stable performance over a wide temperature range. In addition, their long lifespan, generally due to their strong structure, reduces maintenance costs and replacement frequency. These features make industrial type resistors both a cost-effective and reliable option. In high temperature applications and continuous operating conditions, such resistors play an important role in industrial facilities with their reliability and performance.
There are many important factors to consider when choosing a resistor. First, the suitability of the resistor to be used for the application area should be taken into consideration. For example, ceramic resistors are preferred for an application requiring high temperatures, while metal resistors may be sufficient for lower temperatures. Also important is the power capacity of the resistor; Choosing a resistor compatible with the wattage required by your application will ensure that your system operates efficiently.
Another important point is the size and shape of the resistor. The physical dimensions and mounting method of the resistor must be suitable for the area where it will be used. Therefore, a resistor of the correct size and type should be selected according to the residential area. In addition, the material quality and durability of the resistor are also factors to be considered. Resistors made of high quality materials offer long-lasting and less maintenance-requiring solutions. Finally, energy efficiency should also be considered; An efficient resistor reduces energy consumption, reducing costs and reducing environmental impact. Choosing the right resistor by paying attention to these factors will provide great benefits in terms of performance and longevity.
Increasing the energy efficiency of resistors both saves costs and reduces environmental impacts. First, it is important to choose and use resistors correctly. Resistors with wattage and voltage values appropriate to the application area should be preferred. For high efficiency, the appropriate type of resistor should be selected to keep the energy need to a minimum and to transmit heat effectively. Additionally, regular maintenance of the resistor is another important step that increases energy efficiency. Dirty or broken resistors may cause energy loss, so regular cleaning and control should be ensured.
In order to increase the energy efficiency of resistors, attention should also be paid to insulation and thermal insulation. In order to minimize heat loss, using appropriate insulation materials around the resistance reduces energy loss and increases efficiency. Additionally, integrated operation of resistors with control systems can optimize energy use. Intelligent control systems save energy by ensuring that the resistor operates only when necessary. Such systems minimize energy consumption while optimizing the use of resistance, thus providing a more sustainable solution.
Regular maintenance and cleaning of the resistors both extends the life of the device and increases its performance. Maintenance may vary depending on the intended use of the resistor and operating conditions. First, the device must be turned off and unplugged to ensure the safety of electrical connections. Then, dirt and residue accumulated on the surface of the resistor should be gently cleaned with a soft cloth or brush. Water stains and mineral deposits may occur, especially on resistors operating in water vapor or humid environments; Therefore, it needs to be cleaned regularly. Dirt and debris can reduce the efficiency of the resistor and cause energy loss.
During the cleaning process, abrasive cleaners should be avoided. Chemical cleaners or abrasive materials can damage the surface of the resistor and lead to loss of performance in the long term. Instead, it's best to clean using a mild soapy water solution. After cleaning, the resistor should be dried completely and the electrical connection points should be checked. Additionally, regularly checking the area around the resistor and keeping the ventilation holes clean prevents the device from overheating and performance degradation. These simple maintenance and cleaning steps ensure that the resistor operates longer and more efficiently.
The relationship between resistors and heating systems plays a critical role in many areas of modern life. Resistors are components that convert electrical energy into heat, and thanks to these basic features, they are at the heart of heating systems. A heating system usually includes a resistance element; This element creates resistance while passing electric current, and this resistance turns into heat. This heat is transferred to the air, water or other media circulating within the system, thus providing the desired ambient temperature. Electric heaters, water heaters and even some industrial heating systems used in homes work based on this principle.
The use of resistors in heating systems has a great impact on energy efficiency and control. A well-designed heating system ensures that the resistor operates correctly and thus minimizes energy loss. The quality of the resistors directly affects the performance of the heating system. High-quality resistors consume less energy and last longer, reducing costs in the long run. In addition, regular maintenance and appropriate selection of resistors increases the overall efficiency of the system and prevents malfunctions. Therefore, the relationship between heating systems and resistances is critical for both energy saving and long life of the system.
There are several effective ways to extend the life of resistors, and these methods can both improve their performance and reduce maintenance costs. First, the resistor must be used properly and overheating conditions must be avoided. The operating conditions of the resistors must comply with the maximum temperature and voltage limits specified by the manufacturer. Overheating can shorten the life of the resistor and reduce its performance. It is therefore recommended to check heating systems regularly and use protective devices such as thermostats when necessary.
Secondly, regular cleaning and maintenance of the resistor is also important. Dirt and debris on the resistor can affect the heating process and cause the resistor to consume more energy. It is necessary to clean lime and mineral deposits, especially in resistances that come into contact with water, such as water heaters. This cleaning process increases the effectiveness of the resistor and extends its life. Additionally, regular maintenance and checks help detect any wear or faults at an early stage, preventing bigger problems and extending the life of the resistor. These simple but effective steps preserve performance and reduce costs in the long run.
Fill out the form to discover the most suitable high-end products for your projects. Contact Us Now.