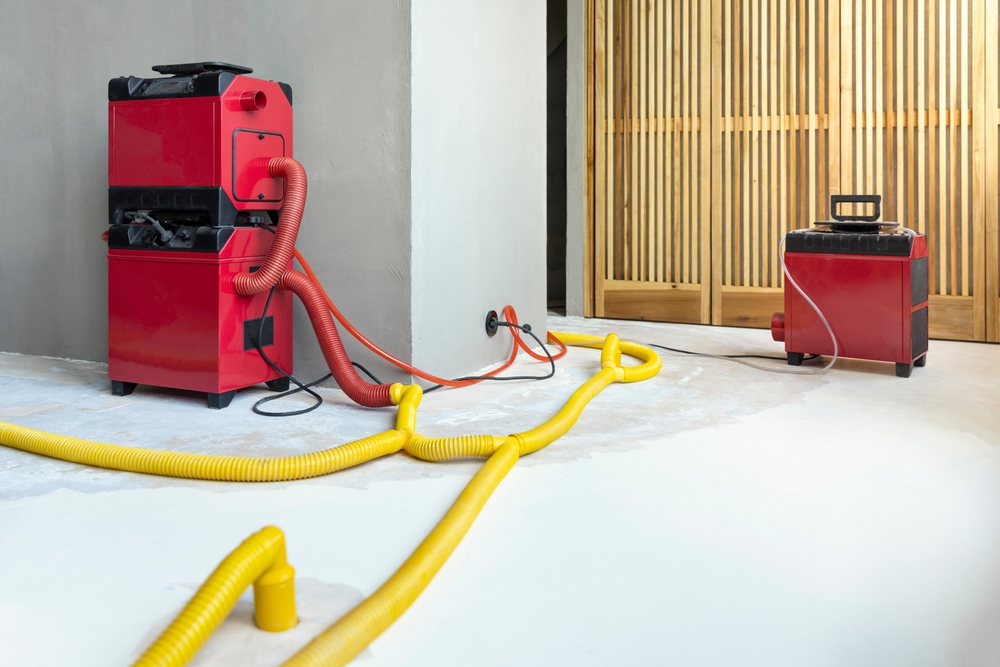
What is Condenser Drying?
When selecting industrial cooling equipment, several key features should be carefully considered to ensure optimal performance and efficiency. First and foremost, it's essential to assess the cooling capacity of the equipment, which is typically measured in BTUs (British Thermal Units) or tons of refrigeration. Understanding your specific cooling requirements based on factors such as the size of the space, heat load, and ambient temperature conditions is crucial in determining the appropriate cooling capacity needed. Additionally, the energy efficiency of the cooling equipment is paramount, as it directly impacts operational costs and environmental sustainability. Look for equipment with high Energy Efficiency Ratio (EER) or Seasonal Energy Efficiency Ratio (SEER) ratings, indicating superior energy performance. Another important factor is the type of refrigerant used in the cooling system, considering both its environmental impact and regulatory compliance. Opt for equipment that utilizes eco-friendly refrigerants with low Global Warming Potential (GWP) and Ozone Depletion Potential (ODP) to minimize environmental harm. Furthermore, consider the durability, reliability, and maintenance requirements of the cooling equipment to ensure long-term performance and minimal downtime. Features such as corrosion-resistant materials, advanced controls for automated operation, and easy access for servicing and repairs can contribute to the overall effectiveness and longevity of industrial cooling systems. By carefully evaluating these key features, businesses can make informed decisions when selecting industrial cooling equipment that meets their specific needs while maximizing efficiency and performance.
Industrial cooling equipment plays a crucial role in enhancing process efficiency in manufacturing by maintaining optimal operating conditions for machinery and equipment. In manufacturing processes, excessive heat can adversely affect the performance and lifespan of machinery, leading to reduced productivity and increased downtime. Industrial cooling equipment helps mitigate these issues by dissipating heat generated during production processes, thereby preventing overheating and ensuring consistent performance of critical equipment. By maintaining the required temperature levels, cooling equipment facilitates precise control over manufacturing conditions, which is particularly vital in industries such as electronics, automotive, and pharmaceuticals, where even minor fluctuations in temperature can impact product quality and integrity. Additionally, efficient cooling systems contribute to energy savings and cost reduction by minimizing the need for manual intervention and optimizing the use of resources. Overall, industrial cooling equipment plays a pivotal role in optimizing process efficiency, enhancing product quality, and maximizing operational productivity in manufacturing environments.
Industrial cooling equipment comes in various types, each tailored to specific industrial needs and applications across different sectors. One common type is air-cooled chillers, which are widely used in industries such as HVAC, food and beverage, and plastics processing. These chillers utilize ambient air to dissipate heat from the refrigerant, making them suitable for outdoor installation and areas where water availability is limited. Another type is water-cooled chillers, which are preferred in industrial settings with high cooling demands and ample water supply. These chillers use water as a cooling medium and are known for their efficiency and reliability, making them suitable for large-scale manufacturing plants and data centers. Additionally, evaporative cooling systems are gaining popularity due to their energy efficiency and environmentally friendly operation. These systems utilize the evaporation of water to lower the temperature of air or process fluids, making them ideal for cooling applications in arid climates and industries such as power generation and chemical processing. Overall, the choice of industrial cooling equipment depends on factors such as cooling capacity, space availability, water availability, energy efficiency, and specific industry requirements.
Industrial cooling systems and traditional air conditioning units serve similar purposes, but they differ significantly in terms of scale, capacity, and application. Traditional air conditioning units are designed for small-scale cooling needs, typically in residential, commercial, or small office spaces. They use a refrigeration cycle to remove heat from indoor air and expel it outside, maintaining a comfortable temperature indoors. In contrast, industrial cooling systems are engineered for large-scale cooling requirements in industrial settings such as manufacturing plants, data centers, and chemical processing facilities. These systems are capable of handling much higher cooling loads and often incorporate more sophisticated components and controls to meet the specific needs of industrial processes. Industrial cooling systems may utilize various cooling technologies such as chillers, cooling towers, and evaporative coolers to achieve efficient cooling across a wide range of industrial applications. Overall, while both types of systems serve the purpose of cooling, industrial cooling systems are designed for heavy-duty use in demanding industrial environments, offering higher capacity, durability, and customization options to meet industrial cooling requirements effectively.
To ensure optimal performance and longevity of industrial cooling equipment, regular maintenance is essential. The maintenance requirements for industrial cooling equipment vary depending on the type of system and its specific components. However, some common maintenance tasks include inspecting and cleaning cooling coils, filters, and condenser fins to remove dirt, debris, and other contaminants that can obstruct airflow and reduce efficiency. Additionally, checking for refrigerant leaks, inspecting electrical connections, lubricating moving parts, and calibrating controls are crucial steps to maintain proper functioning. Regular inspections and preventive maintenance schedules help identify potential issues early, preventing costly breakdowns and downtime. It's also important to follow manufacturer recommendations and guidelines for maintenance procedures to ensure compliance with safety standards and warranty requirements. Overall, proactive and regular maintenance is key to maximizing the performance, efficiency, and reliability of industrial cooling equipment, ultimately optimizing operations and minimizing disruptions in industrial processes.
When investing in industrial cooling equipment, businesses should consider several key factors to ensure they choose the most suitable system for their needs. Firstly, understanding the specific cooling requirements of their operations is crucial. This includes factors such as the size of the space to be cooled, the temperature and humidity levels required, and any specialized cooling needs for particular processes or equipment. Businesses should also evaluate the energy efficiency of the cooling equipment, considering both initial costs and long-term operational expenses. Opting for energy-efficient systems can lead to significant savings on utility bills over time.
Additionally, reliability and durability are essential considerations. Industrial cooling equipment should be robust enough to withstand the demands of continuous operation in challenging industrial environments. Businesses should research the reputation and track record of manufacturers to ensure they provide high-quality, reliable products. Furthermore, compatibility with existing infrastructure and integration with other systems, such as HVAC or process control systems, should be assessed to ensure seamless operation. Finally, businesses should consider factors such as maintenance requirements, warranty coverage, and available technical support when making their investment decisions. By carefully evaluating these factors, businesses can select industrial cooling equipment that meets their needs effectively, contributes to operational efficiency, and provides a solid return on investment.
Fill out the form to discover the most suitable high-end products for your projects. Contact Us Now.