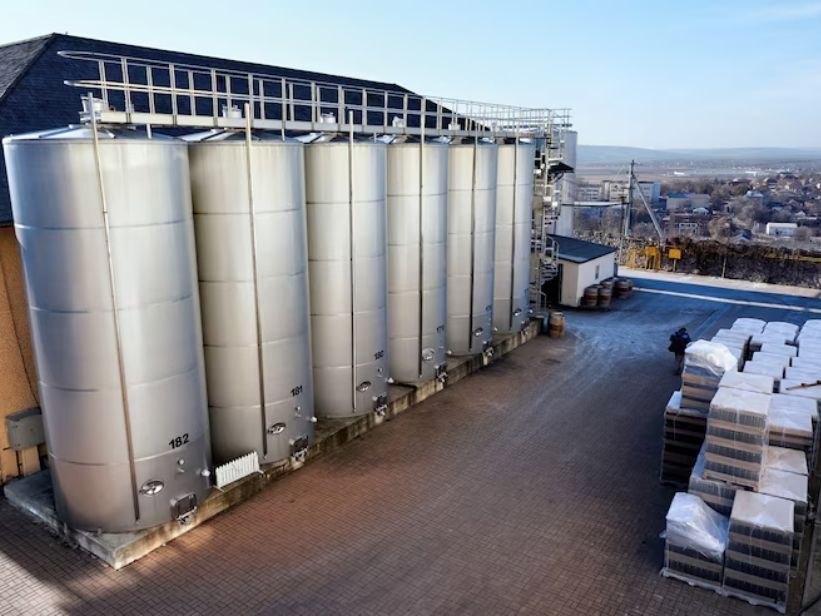
Energy Efficiency in Commercial Condensers: How Does It Reduce Operating Costs?
Efficient condensers are vital components of modern manufacturing systems, serving as the backbone of cooling and heat transfer mechanisms. These devices are critical in managing the temperature of machinery and processes, ensuring that systems operate at optimal levels. With manufacturing processes often generating significant heat, condensers help to dissipate this heat, preventing equipment damage and ensuring continuous, smooth operation. By transferring heat from refrigerants to ambient air or water, efficient condensers make it possible to maintain temperatures within specific parameters, preventing overheating and promoting energy efficiency.
In addition to cooling applications, condensers are fundamental in various industries, from food and beverage production to electronics and pharmaceuticals, where strict temperature control is essential. With the growing demand for sustainability, industries are increasingly turning to energy-efficient condensers that not only provide effective cooling but also help reduce energy consumption and environmental impact.
Efficient condensers are integral to the performance and reliability of manufacturing systems. In sectors such as food processing, where maintaining specific temperatures is crucial to product quality, condensers ensure that temperature-sensitive processes remain within safe limits. Similarly, in chemical manufacturing and pharmaceuticals, temperature regulation is critical for both the safety of operations and the quality of the end product. Without high-performance condensers, equipment could overheat, leading to breakdowns and increased maintenance costs.
Furthermore, condensers help minimize the impact of temperature fluctuations on both the manufacturing process and the environment. For instance, industries that rely heavily on refrigeration and air conditioning for production benefit from condensers that offer consistent cooling performance, even in fluctuating external conditions. The use of these high-efficiency condensers ensures that products are produced under optimal conditions, minimizing waste and maximizing productivity. The result is a more stable, cost-efficient operation that can meet the growing demand for high-quality products in an increasingly competitive marketplace.
There are various types of condensers, each designed to meet different cooling needs based on the specific requirements of the manufacturing process. Air-cooled condensers are one of the most common types and are typically employed in environments where water supply is scarce or unavailable. These condensers rely on ambient air to dissipate the heat absorbed from the refrigerant. They are widely used in small- to medium-sized operations due to their relatively simple design and ease of installation. While they may require more energy to operate compared to water-cooled systems, their lower initial cost and reduced water consumption make them an attractive option for certain applications.
On the other hand, water-cooled condensers are designed to offer more consistent cooling by using water to absorb and remove heat from the refrigerant. These condensers are commonly used in larger facilities or where higher cooling capacities are required, as water can absorb more heat efficiently than air. They are typically employed in large-scale industrial operations such as HVAC systems, refrigeration systems, and large chemical plants. However, water-cooled systems require a continuous water source and are often more complex to maintain than air-cooled systems.
Another increasingly popular option is the evaporative condenser, which combines the features of both air- and water-cooled systems. This type of condenser uses a combination of air and water to enhance the cooling process.
Benefits of High-Performance Condensers
The primary advantage of high-performance condensers is their ability to optimize heat transfer, which directly impacts cooling efficiency and energy consumption. By effectively removing heat from the refrigerant, these condensers ensure that cooling systems operate at peak efficiency, reducing the need for additional energy inputs. This not only lowers electricity costs but also enhances the overall performance of the system, leading to fewer breakdowns and increased equipment lifespan.
Additionally, high-performance condensers contribute to improved temperature stability, which is essential in industries where precision is key. For example, in pharmaceutical manufacturing, maintaining a consistent temperature ensures that products meet stringent quality standards. In food production, temperature control is critical to preserving the quality and safety of products. With the ability to provide consistent and reliable cooling, high-performance condensers ensure that these industries can meet their operational requirements while minimizing waste and product defects.
Energy efficiency plays a crucial role in modern manufacturing, as companies face increasing pressure to reduce their energy consumption and environmental impact. Efficient condensers help manufacturers meet these challenges by offering advanced technology that reduces energy use while maintaining or even improving cooling performance. This reduction in energy consumption can significantly lower operating costs, making it a highly attractive option for companies looking to stay competitive in an energy-conscious world.
Moreover, the environmental impact of condensers is significantly mitigated through the use of eco-friendly refrigerants and cooling methods. Traditional refrigerants used in older systems can have a high global warming potential (GWP), contributing to climate change. In contrast, modern condensers utilize refrigerants with lower GWP, as well as more sustainable cooling techniques, to reduce their environmental footprint.
Choosing the Right Condenser for Your Manufacturing Process
When selecting a condenser for a manufacturing process, it’s important to consider various factors, including cooling capacity, space requirements, and energy efficiency. The size of the condenser must match the heat load generated by the manufacturing equipment, ensuring that the system can handle the cooling demands without excessive energy consumption. For larger operations, water-cooled or evaporative condensers may be more suitable due to their higher cooling capacities, while smaller operations might benefit from air-cooled systems.
Space availability also plays a significant role in condenser selection. Air-cooled systems, for example, require sufficient space for air circulation and heat dissipation, while water-cooled systems need a reliable water source. Manufacturers should carefully evaluate the physical space available in their facilities and choose a condenser that fits within those constraints while still providing optimal cooling performance.
Maintenance and Troubleshooting of Condensers
To ensure efficient operation, regular maintenance is essential for all types of condensers. This includes tasks such as cleaning the coils to remove dirt and debris, checking refrigerant levels, and inspecting the system for any signs of wear and tear. Neglecting maintenance can lead to reduced efficiency, higher energy costs, and potential system failures. Manufacturers should establish a regular maintenance schedule and ensure that trained personnel are responsible for conducting the necessary inspections and repairs.
Troubleshooting is equally important when dealing with condenser performance issues. Common problems include reduced cooling capacity, refrigerant leaks, or abnormal noises. By quickly identifying and addressing these issues, manufacturers can prevent further damage to the system and avoid costly repairs or replacements. For example, a decrease in cooling capacity may indicate a refrigerant leak or clogged coils, both of which can be resolved through routine maintenance or professional servicing.
Fill out the form to discover the most suitable high-end products for your projects. Contact Us Now.