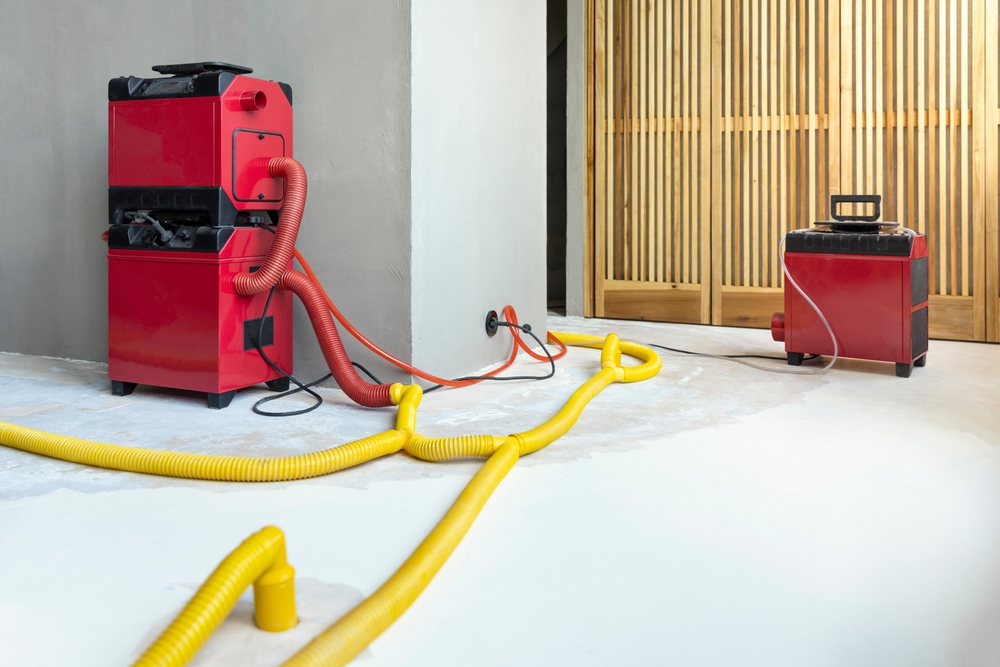
What is Condenser Drying?
Industrial heat exchangers are devices designed to transfer heat between two or more fluids, typically to either cool or heat them. They are widely used in various industrial processes across different sectors such as manufacturing, chemical processing, power generation, and HVAC systems. Heat exchangers operate based on the principle of thermal energy transfer through conduction, convection, or radiation. The basic working principle involves two fluid streams flowing in close proximity but separated by a solid wall. Heat is transferred from one fluid to the other through the wall, without the fluids coming into direct contact, thereby maintaining their respective properties. This exchange of heat enables efficient temperature control, energy conservation, and process optimization within industrial systems. Industrial heat exchangers come in various designs and configurations, including shell and tube, plate and frame, finned tube, and spiral heat exchangers, each tailored to suit specific applications and operating conditions. Overall, these devices play a crucial role in facilitating heat transfer processes essential for the smooth operation of industrial operations while improving energy efficiency and reducing operating costs.
Choosing the right industrial heat exchanger for your application involves several key considerations to ensure optimal performance and efficiency. Firstly, understanding the specific requirements of your process is essential. Factors such as fluid type, flow rate, temperature range, and pressure conditions must be carefully evaluated to determine the most suitable heat exchanger design and materials. For instance, corrosive fluids may require materials with high resistance to corrosion, while high-pressure applications may necessitate robust construction and thicker walls.
Secondly, evaluating the available space and installation requirements is crucial. Different heat exchanger designs have varying footprints and mounting configurations, so it's essential to assess whether the chosen unit can fit within the available space and be installed easily without disrupting existing operations.
Thirdly, considering the long-term maintenance and operational costs is important. Some heat exchanger designs may require more frequent cleaning or maintenance, leading to higher operational expenses over time. Opting for a design with minimal maintenance requirements and a proven track record of reliability can help minimize downtime and overall operating costs.
Additionally, seeking recommendations and expertise from reputable suppliers or consulting with experienced engineers can provide valuable insights into selecting the most suitable heat exchanger for your application. They can offer guidance on design considerations, material selection, and performance expectations based on their industry knowledge and expertise. By carefully evaluating these factors and seeking expert advice, you can make an informed decision and choose the right industrial heat exchanger that meets your specific application needs while ensuring efficient and reliable operation.
Industrial heat exchangers find widespread application across various industries due to their versatile nature and ability to facilitate heat transfer processes efficiently. One of the primary sectors that extensively utilize heat exchangers is the manufacturing industry. These heat exchangers are integral components in equipment and machinery used for metalworking, plastic processing, and other manufacturing processes where precise temperature control is critical for product quality and consistency. Additionally, the chemical processing industry relies heavily on heat exchangers for tasks such as heating, cooling, condensing, and evaporation in chemical reactors, distillation columns, and other processing units. Heat exchangers are also indispensable in power generation facilities, including thermal power plants, where they play a vital role in cooling steam condensers, heating boiler feedwater, and recovering waste heat to improve overall energy efficiency. Other industries such as food and beverage processing, HVAC systems, pharmaceuticals, and automotive manufacturing also utilize industrial heat exchangers for various thermal management applications, underscoring their importance and widespread usage across diverse industrial sectors.
Industrial heat exchangers come in a variety of types, each designed to suit specific applications and operating conditions. One common type is the shell and tube heat exchanger, which consists of a bundle of tubes housed within a cylindrical shell. Fluid flows through the tubes while another fluid passes over the tubes, facilitating heat transfer through the tube walls. Another popular type is the plate heat exchanger, which comprises multiple plates stacked together with alternating channels for the hot and cold fluids. Plate heat exchangers offer high heat transfer efficiency and are compact in size, making them suitable for space-constrained environments. Additionally, there are finned tube heat exchangers, air-cooled heat exchangers, and spiral heat exchangers, each with unique designs optimized for specific applications such as air heating, gas cooling, or liquid-to-liquid heat exchange. The choice of heat exchanger type depends on factors such as operating temperature and pressure, fluid properties, space availability, and desired efficiency, with manufacturers offering a range of options to meet diverse industrial needs.
Industrial heat exchangers are constructed using a variety of materials selected based on their compatibility with the fluids being processed, operating conditions, and cost-effectiveness. Common materials include stainless steel, due to its corrosion resistance and durability, making it suitable for applications involving aggressive fluids or high temperatures. Copper and brass are also popular choices for their excellent thermal conductivity, making them ideal for heat transfer applications. Additionally, titanium is favored for its exceptional corrosion resistance, particularly in highly corrosive environments such as those found in chemical processing industries. For specialized applications, exotic alloys like Inconel and Hastelloy may be used to withstand extreme temperatures and harsh chemical environments. The selection of materials depends on factors such as the nature of the fluids, operating temperatures and pressures, maintenance requirements, and budget considerations, with manufacturers offering a range of material options to meet specific industrial needs.
Industrial heat exchangers play a crucial role in enhancing energy efficiency across various industrial processes. These devices facilitate the transfer of heat between two or more fluids at different temperatures, enabling the recovery and reuse of thermal energy that would otherwise be lost. By efficiently transferring heat from hot process streams to cooler ones, heat exchangers help to minimize energy consumption and reduce the need for additional heating or cooling equipment. This not only conserves energy but also lowers operational costs and environmental impact. Moreover, the use of heat exchangers promotes process optimization by maintaining optimal temperature levels, improving overall system performance, and ensuring consistent product quality. With advancements in heat exchanger design and technology, industries can achieve significant energy savings and sustainability goals while enhancing their competitiveness in the global market.
Fill out the form to discover the most suitable high-end products for your projects. Contact Us Now.