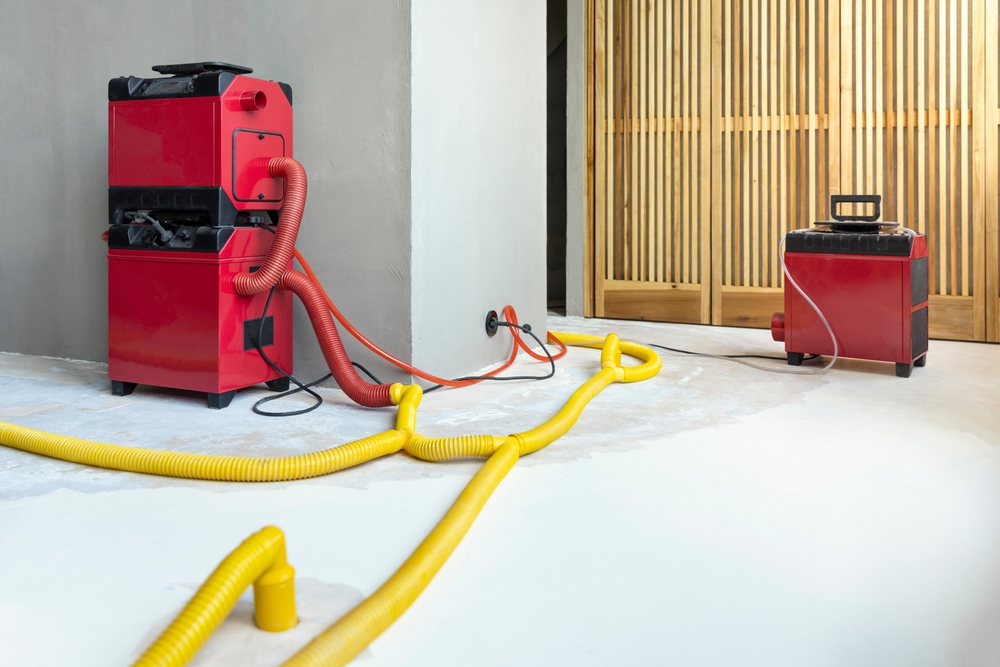
What is Condenser Drying?
There are important features to consider when choosing industrial condenser solutions. First, efficiency is of great importance. An efficient condenser reduces the energy consumption of the business and lowers operating costs. Therefore, a condenser that provides high efficiency should be preferred. However, the size and capacity of the condensers must also be taken into account. A size and capacity that suits the cooling needs of the business must be selected. Additionally, durability and longevity are also an important factor. It is important that condensers to be used in industrial environments are designed to withstand frequent and intense operating conditions. Products from a reliable brand should be preferred and should be expected to provide long-term performance.
There are important features to consider when choosing industrial condenser solutions. First, efficiency is of great importance. An efficient condenser reduces the energy consumption of the business and lowers operating costs. Therefore, a condenser that provides high efficiency should be preferred. However, the size and capacity of the condensers must also be taken into account. A size and capacity that suits the cooling needs of the business must be selected. Additionally, durability and longevity are also an important factor. It is important that condensers to be used in industrial environments are designed to withstand frequent and intense operating conditions. Products from a reliable brand should be preferred and should be expected to provide long-term performance.
Industrial condenser solutions play an important role in optimizing cooling efficiency in manufacturing processes. These solutions increase machine efficiency by keeping businesses' equipment and systems at appropriate temperature levels. In particular, it prevents the uncontrolled spread of high temperatures and reduces malfunctions that may occur due to overheating. Industrial condensers also help reduce energy costs for businesses by increasing energy efficiency. An efficient condenser system optimizes businesses' energy consumption and reduces environmental impact. In addition, regular maintenance and cleaning of industrial condensers increases cooling efficiency and ensures continuous and reliable operation of the business.
Industrial condenser solutions play an important role in optimizing cooling efficiency in manufacturing processes. These solutions increase machine efficiency by keeping businesses' equipment and systems at appropriate temperature levels. In particular, it prevents the uncontrolled spread of high temperatures and reduces malfunctions that may occur due to overheating. Industrial condensers also help reduce energy costs for businesses by increasing energy efficiency. An efficient condenser system optimizes businesses' energy consumption and reduces environmental impact. In addition, regular maintenance and cleaning of industrial condensers increases cooling efficiency and ensures continuous and reliable operation of the business. Therefore, industrial condenser solutions are a critical component to maximize cooling efficiency in the manufacturing industry.
Industrial condenser solutions are widely used across many industries and are designed to meet a variety of process requirements. In particular, the chemical industry is highly dependent on industrial condenser solutions. In chemical production processes, keeping reaction temperatures under control is critical, and condensers are commonly used to cool reactors used in this industry. Additionally, the food processing industry frequently uses industrial condenser solutions. Food products must be kept at certain temperature conditions during the processing process, and therefore refrigeration equipment is needed in food production facilities. Industrial condensers are used in food processing processes to reduce temperature and maintain the quality of products.
Industrial condenser solutions are widely used across many industries and are designed to meet a variety of process requirements. In particular, the power generation industry is significantly dependent on industrial condenser solutions. Power plants rely on condenser systems to cool turbines, and these systems play an important role in electricity production by increasing the efficiency of turbines. Additionally, the pharmaceutical industry also uses industrial condenser solutions. In drug production, reaction temperatures may need to be controlled and products may need to be cooled. Therefore, the use of condensers in pharmaceutical manufacturing facilities is common and critical to ensuring product quality and safety.
There are various industrial condenser solutions for different applications. First, air-cooled condensers are a common option. These types of condensers are systems where air is used directly for cooling and is passed around it via fans to lower the temperature of the vapor or liquid. Air-cooled condensers reduce water usage and are preferred in open areas or areas where water resources are limited. Another option, water-cooled condensers, are systems in which water is processed, absorbs heat and performs the cooling process. Water-cooled condensers provide high efficiency and are preferred in more intensive operations. Additionally, evaporative condensers are also used in different applications. These types of condensers are systems that remove heat through the evaporation of water and are generally used in large facilities or industrial cooling systems.
There are various condenser solutions for different industrial applications. First, air-cooled condensers are a common option. These types of condensers are systems where air is used directly for cooling and is passed around it via fans to lower the temperature of the vapor or liquid. Air-cooled condensers reduce water usage and are preferred in open areas or areas where water resources are limited. Another option, water-cooled condensers, are systems in which water is processed, absorbs heat and performs the cooling process. Water-cooled condensers provide high efficiency and are preferred in more intensive operations. Additionally, evaporative condensers are also used in different industrial applications. These types of condensers are systems that remove heat through the evaporation of water and are generally used in large facilities or industrial cooling systems.
Industrial condenser solutions use a variety of design features and technologies to ensure optimal heat transfer and performance. Primarily, high quality materials and special designs are used for effective heat transfer. These materials have a structure that can transmit heat quickly and efficiently. In addition, properly designing the pipes and channels inside the condensers ensures homogeneous circulation of liquid or vapor, which provides more effective cooling. Additionally, the surface area of condensers is also important because a larger surface area provides greater heat transfer. For this reason, industrial condensers are often designed with arrangements such as cross-flow or tube stacking, which increases the surface area and provides more effective cooling.
Industrial condenser solutions use a variety of design features and technologies to ensure optimal heat transfer and performance. Primarily, high quality materials and special designs are used for effective heat transfer. These materials have a structure that can transmit heat quickly and efficiently. In addition, properly designing the pipes and channels inside the condensers ensures homogeneous circulation of liquid or vapor, which provides more effective cooling. Additionally, the surface area of condensers is also important because a larger surface area provides greater heat transfer. For this reason, industrial condensers are often designed with arrangements such as cross-flow or tube stacking, which increases the surface area and provides more effective cooling. Thanks to these design features, industrial condenser solutions provide optimal heat transfer and performance, increase the efficiency of businesses and help them maintain their operations reliably.
There are many factors that businesses should consider when choosing industrial condenser solutions. First, it is important for businesses to understand their current cooling needs and applications. Each industry may have different cooling requirements, so businesses need to evaluate factors such as process temperature requirements, cooling capacity and continuous operating conditions. Secondly, it is important for businesses to consider their budget and resources. Industrial condenser solutions can have high investment costs, so it is important for businesses to choose a suitable solution by taking their long-term budget and financial planning into consideration. Additionally, energy efficiency should also be considered because energy costs can form a significant part of operating expenses. Finally, it is important for businesses to choose a solution that suits their existing facilities and infrastructure. The installation and integration of industrial condenser solutions must match the structure and requirements of existing facilities, so it is important to select the appropriate equipment. Considering these factors helps businesses choose the most suitable industrial condenser solution and optimize their operations.
There are many factors that businesses should consider when choosing industrial condenser solutions. First, it is important for businesses to understand their current cooling needs and applications. Each industry may have different cooling requirements, so businesses need to evaluate factors such as process temperature requirements, cooling capacity and continuous operating conditions. Secondly, it is important for businesses to consider their budget and resources. Industrial condenser solutions can have high investment costs, so it is important for businesses to choose a suitable solution by taking their long-term budget and financial planning into consideration. Additionally, energy efficiency should also be considered because energy costs can form a significant part of operating expenses. Finally, it is important for businesses to choose a solution that suits their existing facilities and infrastructure. The installation and integration of industrial condenser solutions must match the structure and requirements of existing facilities, so it is important to select the appropriate equipment. Considering these factors helps businesses choose the most suitable industrial condenser solution and optimize their operations.
Fill out the form to discover the most suitable high-end products for your projects. Contact Us Now.