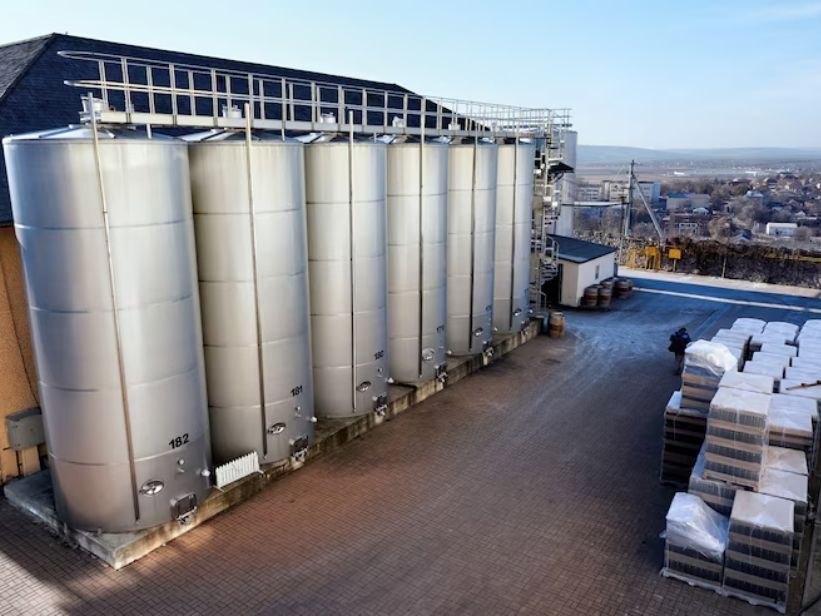
Energy Efficiency in Commercial Condensers: How Does It Reduce Operating Costs?
Choosing the right resistances is a critical aspect of optimizing manufacturing processes. Resistors are vital components that control the flow of electricity and protect delicate equipment from overcurrent, ensuring the proper functioning of electronic systems. Whether in industrial machinery or consumer electronics, the performance and efficiency of these systems largely depend on the quality and specification of the resistances used. Thus, understanding the importance of selecting the right resistances is essential for enhancing productivity and ensuring the longevity of manufacturing equipment.
Selecting the appropriate resistances is not just about cost; it’s also about reliability and long-term performance. The right resistors contribute to smooth production operations, minimize downtime, and prevent damage to sensitive circuits. In addition, they play a crucial role in reducing energy consumption, making them a significant factor in achieving energy-efficient manufacturing processes. The importance of making informed choices when selecting resistors cannot be overstated, as they ensure the seamless operation of complex manufacturing systems that drive industrial production.
Resistance selection impacts the overall efficiency and functionality of manufacturing systems. Inappropriate resistances can lead to poor performance, heat generation, and eventual system failure, disrupting production processes. Ensuring that the resistance values match the system’s requirements guarantees better energy distribution, optimized functionality, and minimal maintenance needs. Proper resistance selection is crucial for sustaining the stability of manufacturing operations over time.
Manufacturers must carefully assess the characteristics of resistors, including power rating, tolerance, and temperature coefficient, to ensure they meet the specific demands of the process. The wrong choice can compromise the safety of the equipment, potentially causing malfunctions and downtime, which could result in increased operational costs and delays. Therefore, meticulous resistance selection should be seen as an investment in the overall productivity and success of a manufacturing operation. The reliability of the entire system relies on the precision with which resistors are chosen, making this process a cornerstone of effective manufacturing.
There are various types of resistors used in manufacturing, each suited for specific industrial applications. Carbon film resistors are commonly used for general-purpose applications, while metal oxide resistors are designed for high-power operations. Wire-wound resistors, known for their accuracy, are ideal for precise measurements and high-precision applications. Choosing the appropriate type of resistor depends on the operating environment, voltage requirements, and power handling capacity.
In industrial processes, resistors are used in a wide range of systems, including control circuits, signal processing equipment, and power regulation devices. The right resistor ensures smooth operation and minimizes the risk of system failure due to power surges or electrical imbalances. As industries continue to evolve, advancements in resistor technology are enabling the development of more specialized and efficient resistors, further enhancing manufacturing processes. For example, in high-performance applications like aerospace or automotive manufacturing, resistors designed to withstand extreme temperatures and pressure variations are critical for ensuring the reliability and safety of the systems they are integrated into.
When selecting resistances, manufacturers need to consider various factors to ensure the best fit for their applications. One of the most critical aspects is the power rating of the resistor, which determines its ability to withstand heat generated by electrical current without failing. Resistance tolerance is another crucial factor, as it dictates how much deviation from the nominal value is acceptable for the application. Temperature stability is also important, as extreme temperatures can cause resistors to change their characteristics, leading to potential performance issues.
Additionally, manufacturers should consider the physical size and form factor of the resistor, as it must be compatible with the circuit board or device it will be used in. For some applications, particularly those involving high frequencies or harsh environmental conditions, special types of resistors, such as surface-mount resistors or high-voltage resistors, may be necessary. Understanding these factors is key to selecting the most appropriate resistances that will optimize both performance and durability. It’s also important to account for potential environmental challenges such as humidity, vibration, and exposure to corrosive elements, which may require resistors with enhanced protection or specialized coatings.
The development of resistance technology has advanced significantly in recent years, allowing manufacturers to achieve higher levels of efficiency and reliability in their operations. Modern resistances are designed to handle more power, function in extreme temperatures, and offer greater precision than ever before. Innovations such as thin-film resistors, which are used in high-precision applications, and digital resistors that allow for more control over resistance values, are just a few examples of how technology has improved the manufacturing process.
These advancements in resistance technology are enabling manufacturers to optimize energy use, improve system longevity, and reduce operational costs. For instance, resistors designed for specific industries, such as automotive or aerospace, are now more durable and versatile, helping to ensure high performance under demanding conditions. With continuous improvements in materials science and electronic design, manufacturers can expect even more efficient and reliable resistances to be integrated into future systems, further boosting productivity and sustainability. The latest innovations also involve the integration of smart technologies into resistors, enabling real-time monitoring and adjustments to ensure optimal performance across a range of industrial applications.
Choosing the right resistances not only affects the performance and cost-efficiency of manufacturing operations but also has significant environmental implications. As manufacturers strive to reduce their carbon footprint, selecting energy-efficient resistors can play a key role in minimizing energy consumption and waste. High-efficiency resistances help decrease the overall energy usage of a system by ensuring that excess energy is not wasted in the form of heat, thus contributing to a more sustainable manufacturing process.
Moreover, the materials used in resistors can also have an environmental impact. Manufacturers are increasingly turning to eco-friendly alternatives, such as resistors made from recyclable or non-toxic materials, to minimize their environmental footprint. By choosing resistances that align with sustainability goals, manufacturers can contribute to both energy efficiency and environmental preservation. This trend is expected to continue as industries increasingly prioritize eco-conscious practices, leading to greener manufacturing solutions worldwide. Additionally, recycling and reusing resistors in industrial processes is becoming more common, contributing to the circular economy and reducing the overall environmental burden of manufacturing operations.
Fill out the form to discover the most suitable high-end products for your projects. Contact Us Now.