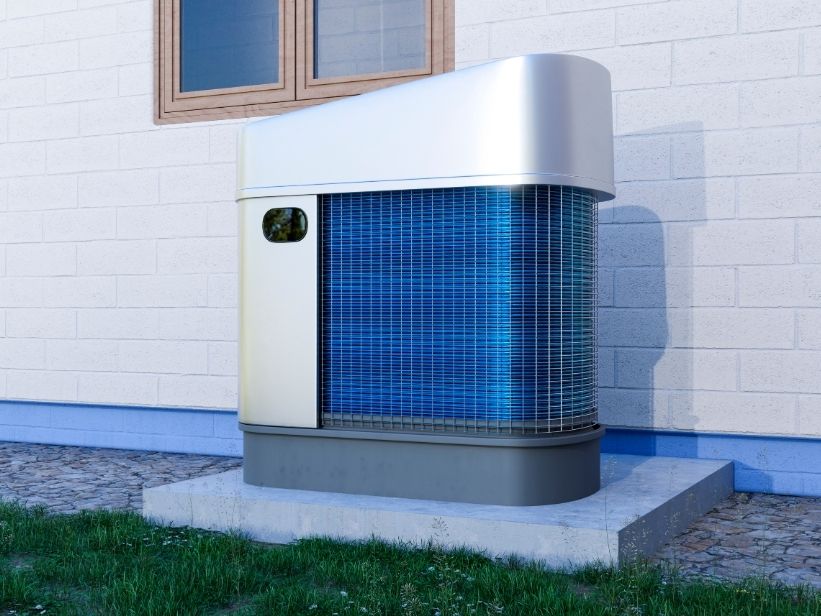
Next Generation Commercial Condenser Technologies: Smarter and Sustainable Solutions
Industrial cooling systems play a critical role as a key element of production processes in many industries. Particularly in the food processing, chemical, pharmaceutical and energy sectors, the proper functioning of cooling systems is indispensable both to maintain product quality and to ensure that production processes continue efficiently and safely. In the food industry, if temperature control is not maintained, products deteriorate rapidly, causing both major economic losses and serious risks to public health. In the chemical industry, correct cooling systems are essential to ensure the stability and effectiveness of products because chemical reactions are often sensitive to heat.
These systems not only protect products but also help businesses manage energy efficiency, sustainability and environmental impact. The correct design of industrial cooling systems provides businesses with high energy savings and significantly reduces operating costs. Modern industrial facilities are constantly developing innovative solutions to minimize the energy consumption of cooling systems and reduce their carbon footprint. Therefore, investments in cooling systems offer businesses not only a cost advantage in the long term, but also the opportunity to fulfill their social responsibilities by displaying an environmentally friendly approach.
One of the most important factors that increase efficiency in industrial cooling systems is related to the selection of the right evaporator and condenser. The evaporator is a critical component in cooling systems that allows the refrigerant to evaporate and absorb heat. This process is the beginning of the cooling process, and a high-efficiency evaporator increases the overall efficiency of the system by absorbing more heat with less energy consumption. On the other hand, the condenser converts the vapor refrigerant back into liquid and releases the heat to the atmosphere. The efficient operation of the condenser ensures that heat is removed from the environment quickly, thus increasing the energetic efficiency of the system.
Since the balance between evaporator and condenser has a direct impact on the overall performance of the system, the selection of both components is very important. This selection should be made according to the characteristics of the sector in which the cooling system will be used. For example, while rapid cooling and low temperature values may be at the forefront in the food industry, high pressure systems may be preferred in the chemical industry. The dimensions of evaporators and condensers should be compatible with the capacity, and efficiency should be ensured by keeping energy consumption to a minimum. A poorly selected evaporator or condenser increases the energy consumption of the system and increases the operational costs of the business.
Therefore, choosing the right device ensures that cooling systems are long-lasting and efficient. New technologies developed for cooling systems enable these components to deliver higher performance with lower energy. In particular, energy efficient evaporators and condensers reduce the environmental impact of businesses and reduce energy costs.
Evaporators are one of the most important components of industrial cooling systems and there are two main types: air-cooled and water-cooled evaporators. While air-cooled evaporators provide cooling with air, water-cooled evaporators provide cooling using water. Water-cooled evaporators generally provide higher efficiency but impose some additional requirements in terms of supplying and managing water.
Evaporator selection should be made according to the facility's climatic conditions, water resources availability and energy efficiency targets. For example, water-cooled evaporators can work more efficiently in regions where water is abundant, while air-cooled evaporators may be more suitable in areas where water is limited. The size of the evaporators also depends on the type of refrigerant used and the cooling capacity. In large facilities, evaporators with larger capacity should be preferred.
Condensers are another critical component of the refrigeration cycle. There are two main types of condensers: air-cooled and water-cooled condensers. While air-cooled condensers allow heat to be removed through air, water-cooled condensers remove heat through water. Water-cooled condensers can generally be more efficient because water has a higher heat carrying capacity. However, there may be difficulties in supplying and managing water.
Condenser selection should be made depending on the capacity of the cooling system, operating conditions and environmental factors. For example, air-cooled condensers may be more effective in hot climates, while water-cooled condensers may be preferred in cold climates. Refrigerants with low GWP values should be used to ensure energy efficiency. Environmentally friendly refrigerants help businesses reduce their carbon footprint.
There are many innovative technologies that increase efficiency in industrial cooling systems. These technologies enable cooling systems to operate more efficiently and save energy. Intelligent control systems, sensors and software constantly monitor the operating conditions of cooling systems and make instant adjustments. This prevents unnecessary energy consumption of the system and optimizes its performance.
Another efficiency-enhancing technology is inverter technology. Inverters save energy by adjusting the motor speed according to the needs of the system. Such technologies enable cooling systems to operate more flexibly and dynamically. It significantly reduces energy consumption by increasing the performance of cooling systems. In this way, businesses can reduce both their costs and environmental impacts.
Energy efficiency is a fundamental criterion in the design of industrial cooling systems. Efficient cooling systems reduce the energy consumption of businesses and minimize their environmental impact. Providing energy efficiency in industrial facilities not only saves costs but also contributes to environmental sustainability by reducing carbon emissions.
Environmentally friendly cooling solutions include the use of refrigerants with low GWP (Global Warming Potential). These refrigerants do not damage the ozone layer and have low global warming potential. Waste heat recovery systems provide additional energy savings by using the excess heat released during cooling processes. Such solutions both reduce the costs of the business and reduce its environmental impact.
Regular maintenance and monitoring are very important to increase the efficiency of cooling systems. Proper functioning of all components of cooling systems helps maintain efficiency. Regular maintenance extends the life of the system and prevents possible malfunctions. Especially in high-capacity systems, monitoring the system allows malfunctions to be detected immediately.
Sensors and smart software used in modern cooling systems facilitate the performance monitoring process. These software detect inefficiencies in the system and increase efficiency by making instant adjustments. Thanks to such technologies, businesses can constantly monitor the performance of their cooling systems and intervene when necessary. Proactive maintenance approaches prevent major malfunctions and reduce maintenance costs.
Efficiency strategies for industrial cooling systems in different sectors are shaped in line with sector-specific needs. For example, while the reliability and efficiency of cooling systems are at the forefront in food processing facilities, the environmental effects and costs of the refrigerants used are important in the chemical industry. Since each industry has different needs and challenges, each business must develop strategies that suit its needs.
Although energy efficiency is a common goal in all sectors, environmental sustainability may be more prominent in some sectors. Especially in environmentally sensitive sectors, applications such as low GWP refrigerants and waste heat recovery are preferred. Efficiency-increasing solutions in industrial cooling systems must be customized for each sector and adapted to the specific requirements of the sector.
Fill out the form to discover the most suitable high-end products for your projects. Contact Us Now.