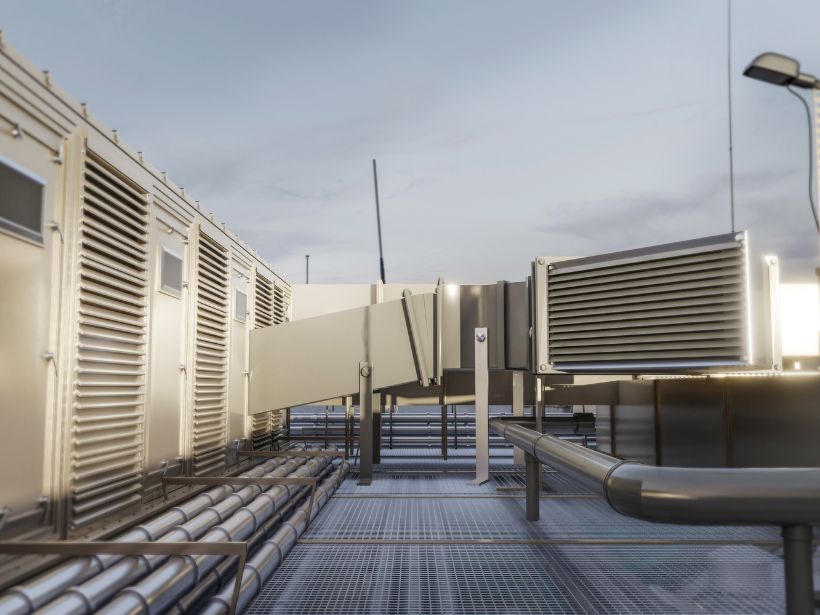
Evaporator Distributor
Condenser maintenance is critical for both energy efficiency and equipment longevity. Regular maintenance ensures condensers operate at optimum performance. A well-maintained condenser transfers heat effectively, which reduces energy consumption and therefore lowers energy bills. Dirty and neglected condensers cause the system to overheat and reduce efficiency. This can lead to both higher energy costs and premature equipment failure.
Additionally, thanks to regular maintenance, small problems can be detected and repaired before they escalate, thus preventing larger and costly malfunctions. This proactive approach reduces system outages and emergencies. Well-maintained condensers also reduce environmental impacts because less energy consumption means lower carbon emissions. This contributes to environmental sustainability and helps the business fulfill its responsibility for the environment.
Condenser cleaning is a critical step in maintaining the effectiveness and efficiency of cooling and heating systems. Cleaning improves the performance of the device and extends its life.
As a first step, turn off the device's power supply and ensure that the system is completely turned off. Disconnecting electrical connections to take safety precautions prevents possible accidents during cleaning. Then, remove all obstacles around the condenser and open the work area to comfortably clean the device. Use a soft brush or vacuum to clean the surface of the condenser from dust and dirt. This process cleans the debris on the fan and heat exchange surfaces. In particular, dirt accumulated on heat exchange surfaces can hinder heat transfer and reduce system efficiency. Carefully cleaning the fan blades ensures that the fan operates effectively.
For deeper cleaning, you can use a hose to apply a gentle spray of water to the outer surface of the condenser. However, be careful that water does not come into direct contact with electrical parts. Avoid keeping the water pressure high as this may damage delicate parts of the device. After cleaning, allow the condenser to dry completely. During cleaning, check for areas that are obstructing air flow or are clogged and clean these areas if necessary. It is also important to replace or clean air filters regularly, as dirty filters restrict airflow and reduce the efficiency of the device. Finally, after all cleaning operations are completed, turn on the power supply of the system again and check whether the device operates normally. Cleaning should be done at regular intervals and should help detect problems that affect the performance of the device in advance. These steps ensure long-lasting and efficient operation of the condenser. Cleaning increases energy efficiency and prevents system failures, which reduces costs and environmental impacts.
Condenser cleaning is a process that must be performed regularly to maintain the efficiency and life of the system. The frequency of cleaning may vary depending on the type of device used, environmental conditions and intensity of use. In general, there are some basic guidelines on how often condenser cleaning should be done.
First, as a general rule, it is recommended that condensers be cleaned at least twice a year. These cleanings are usually done in spring and autumn. Seasonal transitions are periods when the device is more exposed to outdoor conditions and may cause the accumulation of external factors such as dust, dirt and leaves. Therefore, cleaning during these periods ensures that the system works effectively.
More frequent cleaning may be required under heavy use conditions or due to environmental factors. For example, condensers located in industrial facilities or dusty areas may need to be cleaned more frequently. Additionally, in condensers located in dense forests or green areas, the accumulation of leaves and other organic matter may occur more quickly, so the frequency of cleaning should be increased.
Environmental conditions around the condenser also affect the frequency of cleaning. If the condenser is exposed to heavy dust, pollen or polluted air conditions, more frequent cleaning may be required. Considering environmental conditions and adjusting the cleaning frequency according to these conditions maintains the efficiency of the device.
The condenser fan plays a critical role in the efficient operation of cooling and heating systems. Maintenance of the fan and elimination of possible problems directly affects the performance and life of the device. Here are some important things to consider when maintaining and troubleshooting a condenser fan:
Regular maintenance of the condenser fan ensures efficient operation of the system. First, it is important to keep the area around the fan clean. Dust, dirt and other foreign materials accumulated around the fan blades and motor may prevent the fan from working efficiently. Therefore, it is necessary to clean the area around the fan regularly and prevent dust accumulation. Using a soft brush or vacuum, carefully clean the fan blades.
To ensure that the fan blades and motor are working properly, these parts need to be checked regularly. If the fan blades are bent or damaged, this can cause the fan to operate unevenly and cause vibrations. Fixing or replacing bent or damaged blades ensures proper fan operation.
It is also important to check if the fan motor is working properly. If there is abnormal noise or vibration in the sound of the engine, this may indicate that the engine may be worn or needs lubrication. Lubricating the engine's bearings can help the engine run quieter and more efficiently. If there is a problem with the engine itself, it may be necessary to seek help from a professional technician.
Another factor that can affect the performance of the fan is the electrical connections. Make sure cables and connections are tight and secure. Loose connections can cause the fan to run erratically or stop completely. If you see any wear or damage to the electrical connections, it is necessary to repair or replace them.
Regular maintenance on the fan's motor or other parts prevents potential malfunctions and improves the overall performance of the system. Additionally, monitoring the fan's performance helps detect potential problems early. Any abnormality in the fan's performance must be addressed quickly.
Having the correct level of refrigerant directly affects the performance and energy efficiency of the system. Controlling fluid levels is necessary to prevent system failures and ensure long life of the device. Here are the steps to check the condenser refrigerant levels:
First, it is important to ensure the security of the system. Turn off the condenser's power supply and make sure the system is completely turned off. Disconnecting electrical connections ensures a safe working environment and eliminates the risk of possible electric shock.
To check the refrigerant levels, you can use the manometer or pressure gauges included in the system. The manometer next to the condenser measures the pressure of the refrigerant and evaluates this pressure to provide information about fluid levels. The readings seen on the manometer should be compared to the normal ranges specified by the manufacturer.
In order to make accurate pressure gauge readings, you should pay attention to the operating conditions of the system. Cooling systems must generally be tested at a specific operating temperature or load. Under these conditions, pressure gauge readings help you determine correct refrigerant levels.
If the pressure gauge reading shows a value outside the normal range, there may be a problem with the refrigerant levels. Low levels can often be a sign of a leak or leak, so you should check the system for any leaks. Once leaks are detected and repaired, refrigerant levels should be readjusted.
Observation windows or fluid level indicators on the system can also be used. These gauges visibly show the refrigerant level and allow users to quickly assess the situation. However, these indicators may not provide accurate information in all cases, so they should be used in conjunction with pressure gauge readings.
Condenser pipes and connections play a vital role in the efficient operation of cooling and heating systems. Regular maintenance of these components increases the performance of the system and prevents malfunctions. Here are the steps you should consider when maintaining condenser pipes and connections:
First of all, it is important to ensure safety before starting the maintenance process. Turn off the condenser's power supply and make sure the system is completely turned off. Disconnecting electrical connections ensures a safe working environment and eliminates the risk of possible electric shock.
Start by cleaning the outside surfaces of the condenser tubes and connections. You can use a soft brush or damp cloth for this process. Dust, dirt and other foreign matter accumulated on the pipes can hinder heat transfer and reduce the efficiency of the system. You can prevent these deposits by cleaning the surface of the pipes regularly.
Check pipes and connections for leaks. Leaks can cause loss of refrigerant and affect the performance of the system. Whenever you detect any leaks in pipes or connections, you should use appropriate methods to repair these leaks. Repairing leaks and adding the necessary fluid ensures proper operation of the system.
Also check the ports regularly. Situations where ports become loose or worn can cause refrigerant leaks and reduce the efficiency of the system. Make sure connections are tight and secure. If there are loose connections, tighten them or replace fasteners if necessary.
Make sure pipes and connections are properly insulated. Insulation prevents energy loss and increases the efficiency of the system. If there is any damage or wear to the insulating materials, repair or replace them. Proper insulation ensures effective transport of refrigerant.
The heat exchange surfaces of the condenser play a critical role in the efficient operation of cooling and heating systems. These surfaces are designed to provide heat transfer, but they can become dirty over time, which can affect the performance of the system. Here are the steps to be taken into consideration when cleaning and maintaining the heat exchange surfaces of the condenser:
First of all, it is important to ensure safety before starting the cleaning process. Turn off the condenser's power supply and make sure the system is completely turned off. Disconnecting electrical connections ensures a safe working environment and eliminates the risk of possible electric shock.
Before cleaning the heat exchange surfaces, you can use a soft brush or vacuum to remove dust, dirt and other foreign matter that has accumulated on the surfaces. This initial cleaning removes any major dirt and dust from the surfaces. Another important point to consider when cleaning surfaces is the use of high pressure water. A cleaning process with high water pressure may cause deformation or damage of the heat exchange surfaces. Therefore, it is better to keep the water pressure low and do gentle cleaning.
After completing the cleaning process, check the structural integrity of the heat exchange surfaces. If there is any damage or deformation on the surfaces, this may affect the heat transfer efficiency. The fins on the surfaces can be corrected. By making only the necessary corrections, you can maintain the effectiveness of the heat exchange surfaces.
In addition to cleaning and maintenance, heat exchange surfaces need to be checked regularly. Monitoring the performance of the condenser can help you understand whether surfaces are dirty and how efficiency is. Additionally, performance tests and observations allow you to detect if there are any problems with the system.
Leaks in condenser systems can both reduce energy efficiency and affect the performance of the system. Detecting and repairing leaks in a timely manner ensures long life and efficient operation of the system. Here are the steps to detect and repair leaks in the condenser system:
To detect leaks, you first need to perform a visual inspection. Check the exterior of the condenser, pipes and connections for any debris, corrosion or damage. Leaks are often visible in these areas, and visual inspection can help you identify potential leak points.
Another important step is to use appropriate equipment to detect leaks. Refrigerant leak detectors are effective tools for detecting leaks. These detectors can help you identify the presence of leaks where refrigerant comes into contact with air. Additionally, soapy water solutions can also be used. This solution, applied on pipes and connections, creates bubbles at leaks and allows you to visually detect leaks.
Once the leak is detected, you must first power off the system for repair. Disconnecting electrical connections ensures a safe working environment and eliminates the risk of possible electric shock. Clean the area where the leak is located and prepare the necessary materials for repair.
To repair leaks, sealants or welding techniques are often used. If there are minor leaks in the pipes, sealants or special sealing tapes can be used. These materials ensure that the leak is effectively sealed. However, for major leaks or pipe damage, more extensive repairs such as welding or pipe replacement may be required. In such cases, it is best to contact a professional technician.
After repair, ensure that the repaired area is completely dry and the leak is successfully sealed before restarting the system. Before restarting the system, check refrigerant levels and add fluid if necessary.
Before checking the condenser's electrical system, it is important to take safety precautions. Before intervening in the electrical system, turn off the system's power supply. This eliminates the risk of electric shock and ensures a safe working environment. Turn off the main switch on the electrical panels and cut off the power flow by placing a lock if necessary.
As a first step, visually check electrical connections and cables. Check if the cables are frayed, broken or burnt. Also make sure the ports are loose. Loose connections can cause erratic electrical flow and potential malfunction. Tighten or replace cables and connections as necessary.
The next step is to check the fuses and circuit breakers in the electrical panels. Observe for blown fuses or circuit breakers. Blown fuses or circuit breakers may indicate an overload or short circuit in the electrical system. If necessary, replace with appropriate capacity fuses or circuit breakers.
First, the heat exchange surfaces of the condenser need to be cleaned regularly. Dirty or clogged heat exchange surfaces can reduce the efficiency of the system by hindering heat transfer. Cleaning dust and dirt on surfaces increases heat transfer and reduces energy consumption. It is important to use appropriate cleaning materials and techniques for the cleaning process.
Optimizing airflow around the condenser can also increase efficiency. Obstacles or obstructions around the condenser can restrict airflow, affecting the performance of the system. Therefore, keeping the area around the condenser clean and open allows airflow to pass freely. Also make sure fans and airflow diverters are working properly.
Using energy efficient fans can improve the performance of the condenser. Modern, energy-efficient fans provide higher airflow with lower energy consumption. Regular maintenance of fan motors and replacement when necessary increases the efficiency of the system. Additionally, controlling the speed of fans and using variable speed fan systems optimizes energy consumption.
It is important to check refrigerant levels regularly and add as needed. Low refrigerant levels can affect the efficiency of the condenser and increase energy consumption. Adjusting refrigerant levels correctly ensures optimum performance of the system.
Improving the insulation of the condenser can also increase efficiency. Insufficient insulation can cause heat loss and increase energy consumption. Strengthening the insulation of the condenser reduces energy loss and increases the efficiency of the system.
It is also important to perform regular maintenance and performance tests to monitor system performance. Periodic maintenance detects potential problems in the system early and provides regulations that increase efficiency. Additionally, performance tests are used to evaluate the energy consumption and efficiency of the system.
Finally, choosing the capacity of the condenser to suit system needs can increase efficiency. A condenser of appropriate capacity optimizes the energy efficiency of the system and increases its performance. Make sure the capacity of the condenser meets the system requirements.
In short, to increase the efficiency of the condenser, improvements such as cleaning the heat exchange surfaces, optimizing the air flow, using energy efficient fans, controlling the refrigerant levels, improving the insulation, performing regular maintenance and performance tests and selecting the appropriate capacity can be applied. These steps increase the energy efficiency of the condenser and optimize system performance.
Condenser maintenance must be done carefully for high performance and safety. First, before starting maintenance, it is a critical step to completely turn off the system's power supply. To avoid the risk of electric shock, it is necessary to disconnect the device from the electrical connections. This ensures a safe working environment and prevents possible electrical accidents.
The use of personal protective equipment is another important factor that increases safety. Equipment such as glasses, gloves, protective clothing and safety shoes provide protection against hazards that may be encountered during maintenance. In particular, it is necessary to use appropriate protectors to reduce the possibility of contact with chemicals or dust.
Extra care should be taken when working with refrigerants. These chemicals can leak and cause health problems. Therefore, when checking for leaks of refrigerants or making changes, you must use protective equipment and follow safe working methods.
Condensers generally operate under high temperature and pressure. During maintenance under these conditions, care should be taken to avoid direct contact with hot surfaces and care should be taken when intervening in pressurized systems. Temperature and pressure control contributes to the safe maintenance process.
It is important that only personnel with the necessary training and authority perform maintenance operations. Trained technicians accurately assess potential hazards and ensure a safe maintenance process. In addition, regular inspection of vehicles and equipment used during maintenance is necessary to prevent possible accidents. Damaged or malfunctioning vehicles can increase safety risks.
Fill out the form to discover the most suitable high-end products for your projects. Contact Us Now.