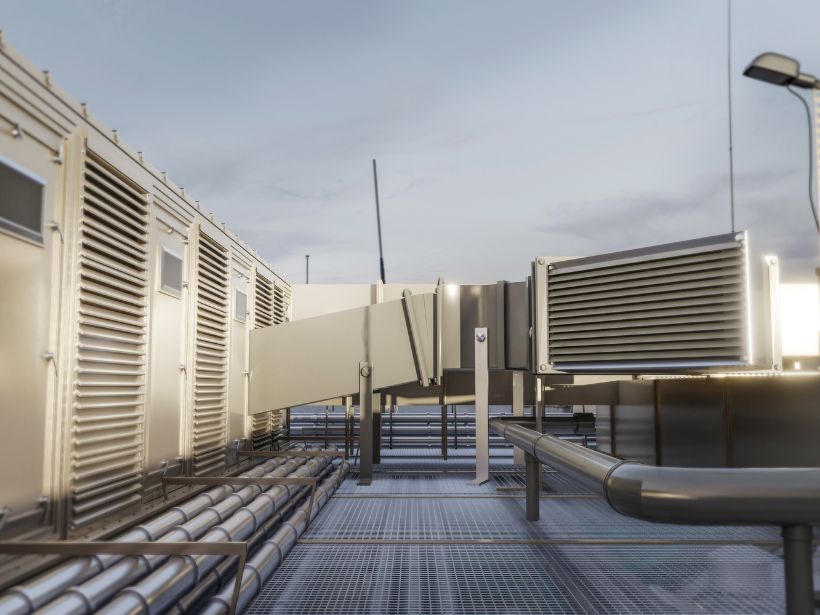
Evaporator Distributor
Defrost resistor solutions play a critical role in refrigeration systems, particularly in applications such as commercial freezers, industrial refrigeration, and HVAC systems. These resistors are essential for preventing ice buildup on evaporator coils, ensuring consistent performance and extending the lifespan of refrigeration equipment. Effective defrost resistor solutions contribute to improved energy efficiency, reduced maintenance costs, and enhanced overall system reliability.
Defrost resistor solutions are available in various types, each designed to meet specific applications and technical requirements. The most common types include electrical defrost resistors, thermal defrost resistors, and integrated defrost systems. Electrical defrost resistors use electrical current to generate heat, effectively melting ice on the evaporator coils. Thermal defrost resistors rely on ambient temperature changes and thermal conductivity to initiate the defrost process. Integrated defrost systems combine both electrical and thermal methods to optimize defrost cycles and enhance system efficiency.
The effectiveness and durability of defrost resistor solutions heavily depend on the quality of materials used and the precision of manufacturing processes. Materials such as nichrome wire, ceramic insulators, and high-grade metals ensure optimal heat generation and resistance to corrosion. Advanced manufacturing techniques, including precision winding and automated assembly, contribute to the production of reliable and high-performance defrost resistors. Additionally, stringent quality control measures and performance testing guarantee that each resistor meets the highest industry standards.
In today's environmentally conscious market, energy efficiency and sustainability are paramount in the design and implementation of defrost resistor solutions. Modern resistors are engineered to maximize heat output while minimizing energy consumption through the use of energy-efficient materials and optimized heating elements. Sustainable manufacturing practices, including the use of recyclable components and the implementation of waste reduction strategies, aim to reduce the environmental impact of production processes. This focus on energy efficiency not only lowers operational costs but also supports global sustainability goals.
Continuous innovation and investment in research and development are essential for advancing defrost resistor technology. Innovations such as smart defrost control systems and IoT (Internet of Things) integration enhance the functionality and efficiency of defrost processes. Additionally, advancements in heater design and thermal management improve performance and extend the lifespan of defrost resistors. R&D efforts also focus on developing new materials and manufacturing techniques to create more efficient, durable, and environmentally friendly defrost resistor solutions.
Each refrigeration system and application has unique requirements, making customized defrost resistor solutions essential. Manufacturers collaborate closely with clients to design and engineer resistors that meet specific thermal, spatial, and operational needs. This collaborative approach involves detailed consultations, precise design modifications, and tailored manufacturing processes. Ensuring customer satisfaction through personalized solutions fosters long-term partnerships, drives repeat business, and generates positive referrals.
In the competitive global market, effective marketing strategies are crucial for defrost resistor solution providers. Building a strong brand presence through digital marketing, participation in industry trade shows, and obtaining international certifications can significantly enhance market visibility. Additionally, understanding and adapting to regional market trends and regulatory requirements enable manufacturers to cater to diverse customer bases and maintain a competitive edge on a global scale.
Providing comprehensive maintenance and service support is integral to the success of defrost resistor solutions. Regular maintenance ensures that resistors operate efficiently and extend their service life. Service support includes scheduled inspections, troubleshooting, and replacement of worn-out components. Offering prompt and reliable service enhances customer trust and satisfaction, positioning the manufacturer as a dependable partner in the industry.
Adhering to international industrial standards and obtaining relevant certifications are critical for ensuring the quality and reliability of defrost resistor solutions. Certifications such as ISO 9001, CE, and UL validate that the resistors meet specific quality, safety, and performance criteria. Compliance with these standards not only reassures customers of product reliability but also facilitates access to global markets and fosters trust in the brand.
Efficient logistics and supply chain management are essential for the timely delivery and installation of defrost resistor solutions. Effective coordination with suppliers, optimized inventory management, and streamlined distribution processes minimize delays and reduce operational costs. Additionally, leveraging advanced logistics technologies, such as inventory management software and real-time tracking systems, enhances the overall efficiency and reliability of the supply chain.
The expertise and skills of the workforce are fundamental to the innovation and quality of defrost resistor solutions. Investing in the continuous training and development of engineers, technicians, and production staff ensures that the team stays updated with the latest technological advancements and industry best practices. A knowledgeable and skilled workforce drives the creation of innovative solutions and maintains high standards of quality and efficiency.
Robust financial management is crucial for the sustainable growth and expansion of defrost resistor solution manufacturers. Effective financial planning involves allocating resources for research and development, production capacity expansion, and marketing initiatives. Strategic investments in technology and infrastructure enhance operational capabilities and drive long-term success. Additionally, prudent risk management practices safeguard the company against economic fluctuations and market uncertainties.
Compliance with various regulations and legal requirements is essential for operating within the global market. Adhering to environmental regulations, safety standards, and industry-specific laws ensures that defrost resistor solutions are not only effective but also environmentally responsible and safe to use. Staying informed about changing regulations and proactively adjusting operations accordingly helps maintain compliance and avoids legal complications.
Integrating advanced technologies into defrost resistor solutions significantly enhances their functionality and performance. Smart sensors and automation systems enable real-time monitoring and control, optimizing heat transfer processes and improving energy efficiency. Additionally, leveraging data analytics and machine learning facilitates predictive maintenance and operational optimization, ensuring that defrost resistors operate at their highest potential.
Forming strategic partnerships with global suppliers allows defrost resistor solution manufacturers to access high-quality materials and cutting-edge technologies. Collaboration with reputable suppliers enhances product quality and accelerates innovation processes. Moreover, maintaining strong relationships with suppliers ensures a reliable supply chain, enabling manufacturers to meet customer demands efficiently and maintain a competitive advantage in the market.
Customer feedback plays a vital role in the continuous improvement of defrost resistor solutions. Insights from users provide valuable information for refining product designs, enhancing functionality, and addressing any performance issues. Actively seeking and analyzing customer feedback allows manufacturers to make informed decisions, tailor solutions to meet evolving needs, and ensure high levels of customer satisfaction and loyalty.
Staying ahead of future trends is essential for defrost resistor solution providers to maintain their competitive edge. Emerging trends such as renewable energy integration, energy-efficient designs, and smart grid technologies are shaping the future of defrost resistor technology. Additionally, advancements in materials science, nanotechnology, and artificial intelligence are driving innovations that enhance the performance and sustainability of defrost resistor solutions. By anticipating and adapting to these trends, manufacturers can continue to deliver state-of-the-art solutions that meet the evolving needs of various industries and maintain their leading positions in the market.
Fill out the form to discover the most suitable high-end products for your projects. Contact Us Now.