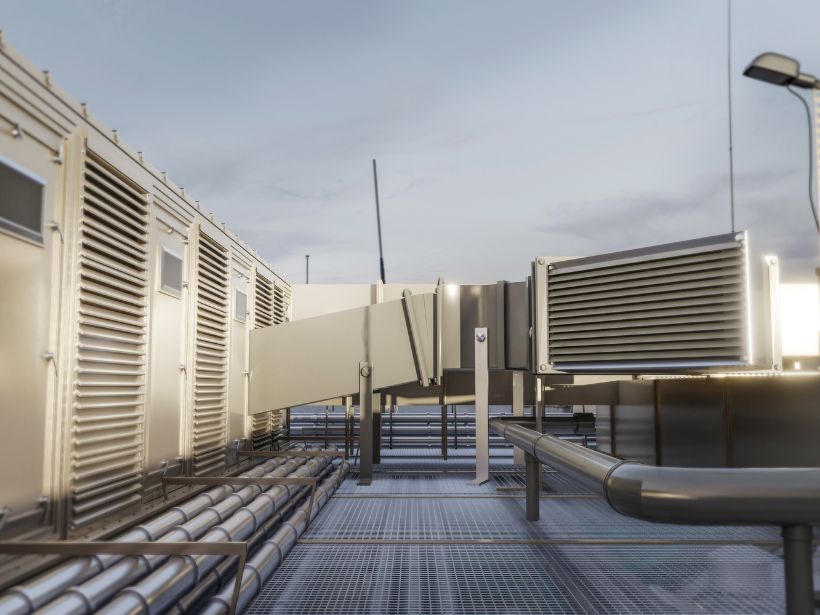
Evaporator Distributor
When selecting a condenser manufacturer, several key criteria should be considered to ensure the optimal performance and reliability of the condenser unit. Firstly, it's essential to assess the manufacturer's reputation and track record in the industry. Researching customer reviews, testimonials, and case studies can provide insights into the manufacturer's reliability, product quality, and customer satisfaction levels. Additionally, evaluating the manufacturer's experience and expertise in condenser design, engineering, and manufacturing is crucial. A manufacturer with extensive experience and specialized knowledge in condenser technology is more likely to deliver high-quality products that meet specific application requirements.
Another important criterion is the manufacturer's adherence to industry standards and certifications. Ensure that the manufacturer complies with relevant industry standards such as ASME, ISO, or API, which guarantee the quality, safety, and performance of the condenser units. Moreover, consider the manufacturer's ability to customize condenser solutions to meet unique project requirements. A manufacturer that offers flexible design options, custom engineering capabilities, and tailored solutions can better address the specific needs and challenges of each application. Additionally, evaluating the manufacturer's technical support, after-sales service, and warranty offerings is essential for ongoing support and maintenance of the condenser unit throughout its lifecycle. By carefully considering these criteria, industrial users can select a condenser manufacturer that offers reliable, high-performance solutions tailored to their specific needs and requirements.
Collaborating with a condenser manufacturer offers several advantages for industrial users seeking reliable and efficient cooling solutions. Firstly, condenser manufacturers typically possess specialized expertise and experience in condenser design, engineering, and manufacturing. By leveraging their knowledge and skills, industrial users can benefit from customized condenser solutions tailored to their specific application requirements. Manufacturers can offer valuable insights and recommendations on the most suitable condenser design, materials, and configurations to optimize performance, energy efficiency, and operational reliability.
Secondly, partnering with a condenser manufacturer provides access to advanced technologies and innovative solutions. Manufacturers often invest in research and development to enhance their product offerings and stay abreast of industry trends and advancements. By collaborating with a manufacturer at the forefront of technological innovation, industrial users can access cutting-edge condenser technologies that offer improved performance, efficiency, and sustainability. Additionally, condenser manufacturers typically provide comprehensive technical support, customer service, and after-sales assistance. This ensures seamless integration, installation, and operation of the condenser unit, as well as ongoing maintenance, troubleshooting, and parts replacement services as needed. Overall, cooperating with a condenser manufacturer offers industrial users access to expertise, innovation, and support to meet their cooling needs effectively and efficiently.
Condenser manufacturers serve a diverse range of industries that rely on efficient cooling systems for their operations. One prominent sector is the power generation industry, where condensers play a vital role in steam turbine power plants. These condensers extract heat from steam exiting the turbine, converting it back into liquid form for re-circulation, thus improving the overall efficiency of power generation. Another key industry is the chemical processing sector, where condensers are used in various processes such as distillation, solvent recovery, and chemical synthesis. Condensers help cool and condense vaporized chemicals, enabling separation and purification of different components in chemical mixtures.
Additionally, condenser manufacturers cater to industries such as petroleum refining, where condensers are integral to processes like oil refining, gas processing, and petrochemical production. In HVAC (heating, ventilation, and air conditioning) systems, condenser units are essential for cooling refrigerants in air conditioning and refrigeration applications across residential, commercial, and industrial buildings. Furthermore, condenser manufacturers serve industries such as food and beverage processing, pharmaceutical manufacturing, and automotive manufacturing, where cooling systems are essential for maintaining product quality, process efficiency, and equipment performance. Overall, condenser manufacturers play a crucial role in supporting a wide array of industries by providing reliable and efficient cooling solutions tailored to their specific needs and applications.
Condenser manufacturers offer a variety of products and services to meet the diverse cooling needs of their customers across different industries. One primary product offered by condenser manufacturers is the condenser unit itself, available in various configurations such as shell-and-tube, plate, or air-cooled condensers. These units are designed to efficiently transfer heat and condense vapor into liquid form, essential for processes like power generation, chemical processing, HVAC systems, and more. Additionally, condenser manufacturers may provide custom-engineered solutions tailored to specific project requirements, offering flexibility in design, material selection, and performance specifications.
In addition to manufacturing condenser units, condenser manufacturers often offer a range of associated products and services to support their customers throughout the entire project lifecycle. This includes engineering and design services to assist with system layout, sizing, and integration into existing processes. They may also provide installation, commissioning, and maintenance services to ensure proper operation and longevity of the condenser units. Furthermore, condenser manufacturers may offer spare parts, retrofitting, and upgrade services to extend the lifespan and enhance the performance of existing condenser systems. Overall, condenser manufacturers strive to deliver comprehensive solutions encompassing products, engineering expertise, and support services to meet the cooling needs of various industries effectively.
Condenser manufacturers ensure the quality of their products through a combination of rigorous quality control processes, advanced manufacturing techniques, and adherence to industry standards. One key aspect is the use of high-quality materials and components sourced from reputable suppliers. Manufacturers carefully select materials such as stainless steel, copper, or aluminum alloys known for their corrosion resistance, thermal conductivity, and durability. Additionally, condenser manufacturers employ state-of-the-art manufacturing processes and technologies to ensure precision, consistency, and reliability in the production of condenser units. This includes advanced welding techniques, precision machining, and automated assembly lines to minimize defects and ensure product quality.
Moreover, condenser manufacturers implement stringent quality control measures at every stage of the manufacturing process, from raw material inspection to final product testing. This includes comprehensive material testing, dimensional checks, pressure testing, and performance validation to verify conformance to design specifications and industry standards. Additionally, manufacturers often undergo certifications and audits by independent organizations such as ISO (International Organization for Standardization) or ASME (American Society of Mechanical Engineers) to demonstrate compliance with quality management systems and regulatory requirements. By prioritizing quality at every step of the manufacturing process, condenser manufacturers ensure that their products meet the highest standards of performance, reliability, and longevity, ultimately delivering value and satisfaction to their customers.
Condenser manufacturers utilize a variety of technologies to design, engineer, and manufacture efficient and reliable condenser units. One of the primary technologies employed is computer-aided design (CAD) and modeling software, which allows engineers to create detailed 3D models of condenser components and systems. CAD software enables precise design iterations, optimization of thermal performance, and integration of complex features such as fins, tubes, and baffles for enhanced heat transfer. Additionally, manufacturers utilize computational fluid dynamics (CFD) simulations to analyze fluid flow patterns, heat transfer characteristics, and pressure distributions within condenser units. CFD simulations help optimize the design of heat exchanger surfaces, improve thermal efficiency, and minimize pressure drop across the system.
Furthermore, condenser manufacturers leverage advanced manufacturing technologies such as CNC (computer numerical control) machining, laser cutting, and robotic welding to ensure precision and consistency in component fabrication. These technologies enable tight tolerances, intricate geometries, and high-quality finishes, resulting in reliable and durable condenser units. Additionally, manufacturers may employ advanced materials and coatings technologies to enhance the corrosion resistance, thermal conductivity, and durability of condenser components. For example, nanostructured coatings or corrosion-resistant alloys can improve the performance and longevity of condenser tubes in harsh operating environments. Overall, condenser manufacturers harness a range of advanced technologies to deliver innovative, high-performance condenser solutions that meet the demanding requirements of various industrial applications.
Fill out the form to discover the most suitable high-end products for your projects. Contact Us Now.